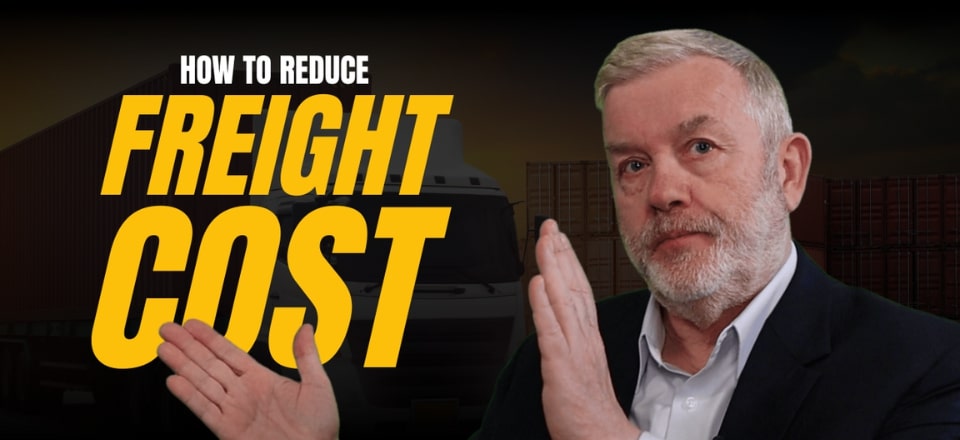
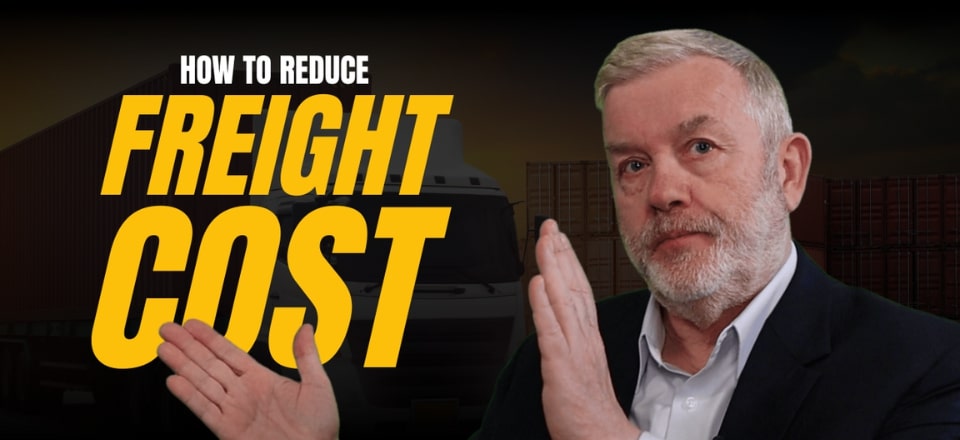
Follow Logistics Bureau
Recent Posts
- What is Procure to Pay (P2P) – What is Procurement to Payment?
- What does Corporate Social Responsibility Really Mean?
- Why Large Companies Increasingly Opt for 4PL Services
- Definitions for Supply Chain & Logistics – LLP, 3PL, 4PL and More
- Warehouse Capacity FIX – What Works
- How to Reduce Warehouse Costs with Warehouse Product Slotting
- Warehouse Capacity – How to Increase It and Avoid Moving
Categories
- 3PL
- 4PL
- 5PL
- Articles
- Benchmarking
- Business thoughts
- Career Tips
- Charity Work
- Cost Saving
- Cost to Serve
- Cost to Supply
- Distribution Centre
- Distribution Channels
- Distribution Network Design
- Events
- Freight Management
- HR / People
- Leadership
- Logistics Bureau Videos
- News
- operations
- Performance Measurement – KPIs
- procurement
- Procurement – Purchasing – SRM
- Purchasing
- SC
- SRM
- Supply Chain
- Supply Chain Education Programs
- Trends
- Videos – Other
- Videos-SCM
- warehouse